About
FRP Technologies
About
FRP Technologies
Established in 2001, F R P Technologies (Pvt) Ltd is a frontrunner in Marine, Automotive, and Construction sectors. Today, we’re poised to dominate the global FRP industry with cutting-edge products. Led by a dynamic team of young professionals, we’re set to become Asia’s first Carbon Fiber Wind Turbine Rotor Manufacturer. Backed by a major Chinese conglomerate, our 2010 partnership with WIND ASIA propelled us into wind turbine rotor manufacturing and repair for the Asian market.
Additionally, we’re renowned for manufacturing premium seating and components for OEM vehicles, stadiums, and auditoriums worldwide. At FRP Technologies, we’re committed to pioneering excellence and shaping the future of FRP technology.
Our Team
Our company is led by a strong management team. Dimantha Jayawardena and Chamath Tennakoon collectively drive our company towards success and industry leadership.
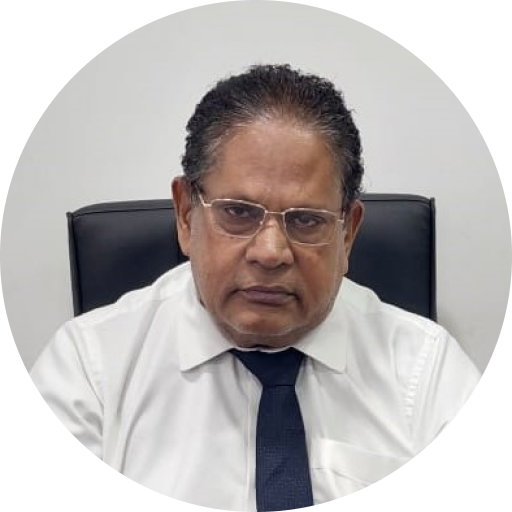
Ivan Perera
Chairman
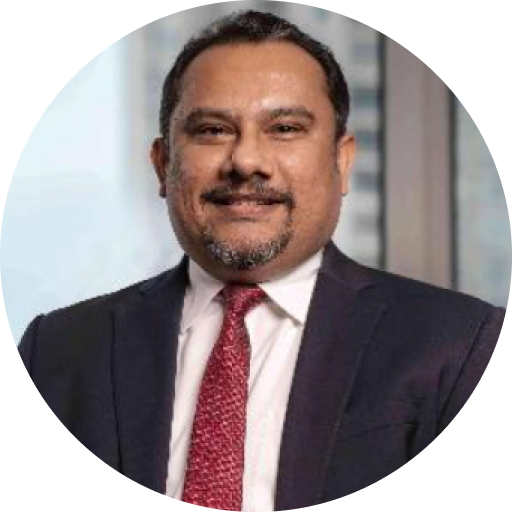
Dimantha Jayawardena
Managing Director
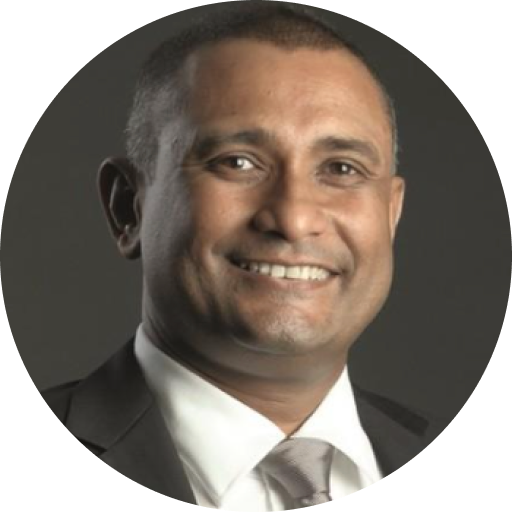
Chamath Tennekoon
Group Chief Executive Officer
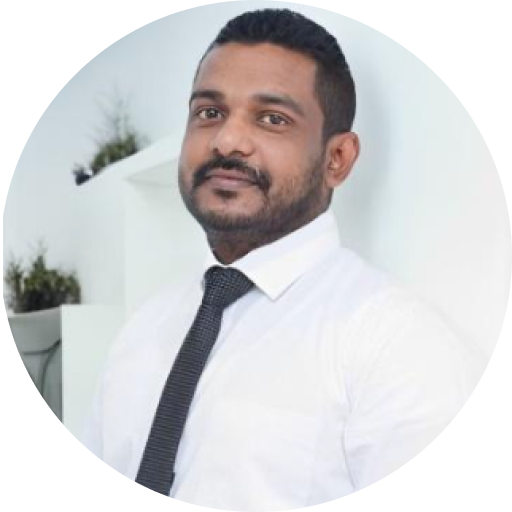
Mahendra Wanasinghe
Deputy General Manager
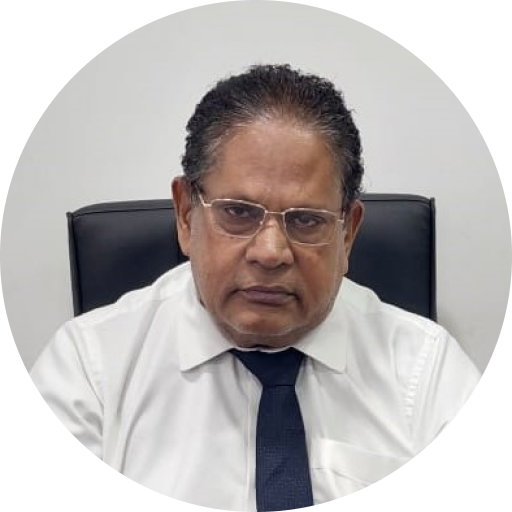
Ivan Perera
Chairman
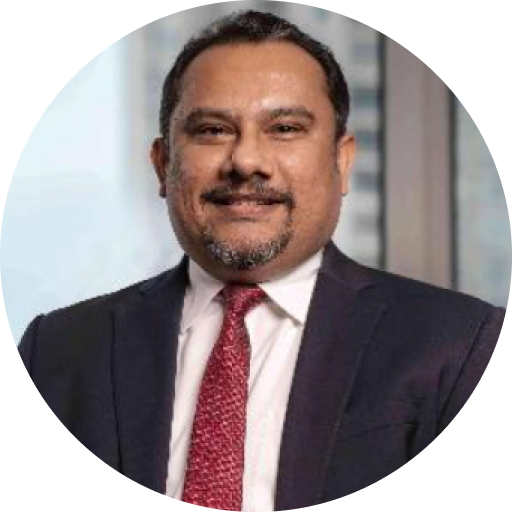
Dimantha Jayawardena
Managing Director
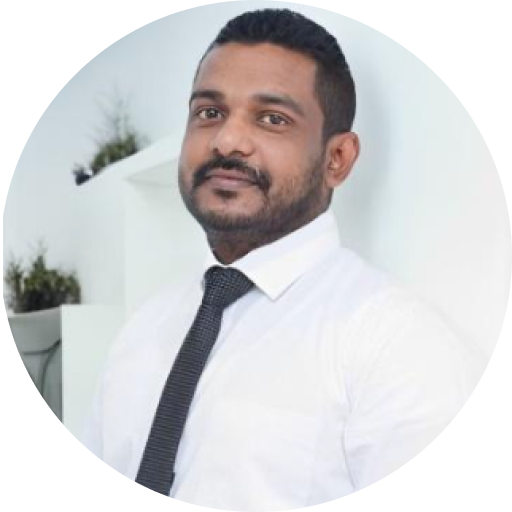
Mahendra Wanasinghe
Deputy General Manager
Our Features
Advanced Fiberglass Manufacturing. Precision Components for Automotive and Marine Industries.
Design & Engineering
Our industry-affiliated engineers have solved challenges that other companies said were impossible, Designing and engineering solutions that bring to life the dreams and designs of artists, architects and design professionals across the globe. We have extensive civil and composite engineering abilities – including FEA, Harmonics, Hydrostatics, and Mechanical. This depth and breadth of design and engineering talent helps us gives our customers a significant competitive edge.
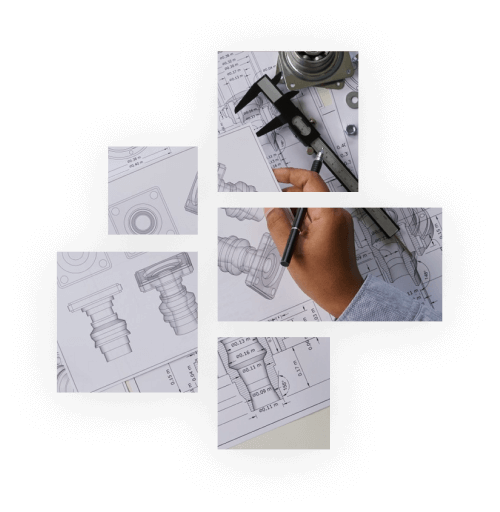
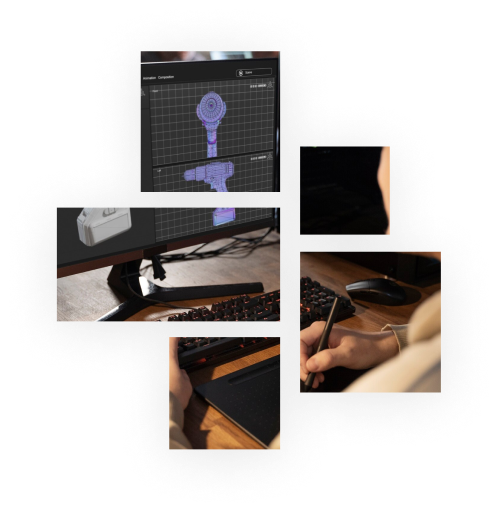
Tooling & Prototyping
PROTOTYPING
MouldCAM’s prototyping specialists can develop durable, functional prototypes that allow customers to test, troubleshoot and refine designs and fix unexpected problems before production commences. The cost-savings, in terms of time and money, can be significant
TOOLING
In the production stage, our engineers tightly monitor the tool and pattern process to ensure the composite molds produced are of the highest quality, with impeccable dimensional accuracy
Project Management
Our project managers have proven skills across a range of high value and complex projects and work with customers worldwide to deliver on time and within budget. They analyse and track schedules, plan labour and material resources, administer costs, and provide complete visibility, informed advice and real time project updates at every stage. Many of our customers we have worked with over many years and on multiple projects. They continue to select mouldCAM as their Computer Aided Manufacturing partner because of our consistent track record for on time, on budget delivery.

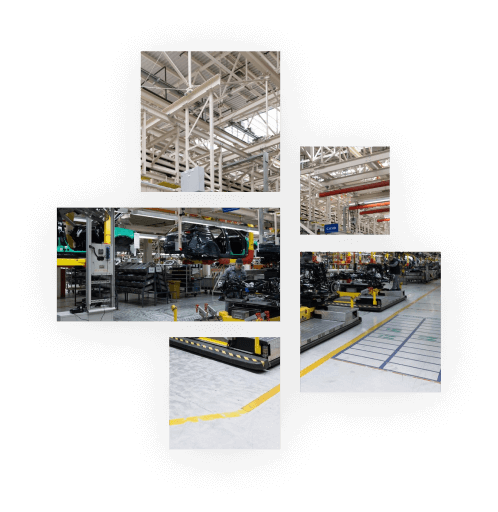
Manufacturing Facilities
FRP Technologies operates manufacturing and engineering facilities in the China and Sri Lanka with a combined production capacity of over 6,300 square meters/67,813 square feet.
- 2D & 3D profiling
- Free form and solid
- CAD modelling and drafting
- Reverse Engineering
- 5 axis CNC pattern machining
- GRP plugs, composite molds and composite tooling
- Vacuum infusion
- Prototype development
- Parts production runs
Prepreg manufacturing - High temperature curing
- Assembly and fit out
- Spray painting and lacquering
- Custom packing, shipping
- Closed molding RTM manufacturing
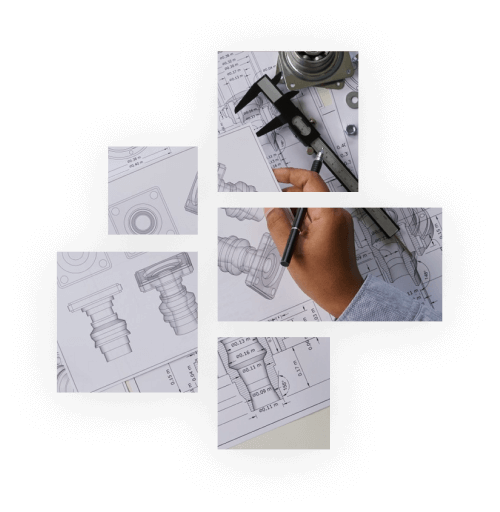
Design & Engineering
Our industry-affiliated engineers have solved challenges that other companies said were impossible, Designing and engineering solutions that bring to life the dreams and designs of artists, architects and design professionals across the globe. We have extensive civil and composite engineering abilities – including FEA, Harmonics, Hydrostatics, and Mechanical. This depth and breadth of design and engineering talent helps us gives our customers a significant competitive edge.
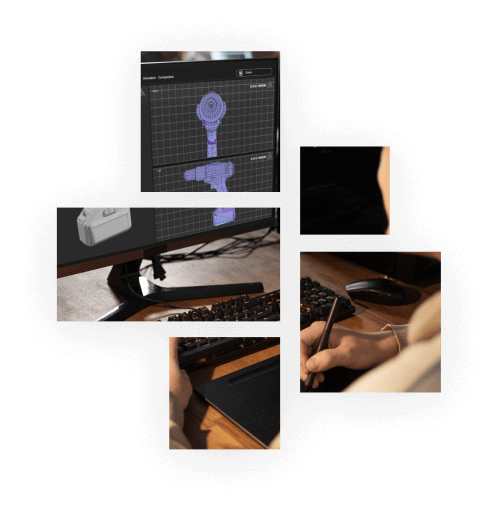
Tooling & Prototyping
PROTOTYPING
MouldCAM’s prototyping specialists can develop durable, functional prototypes that allow customers to test, troubleshoot and refine designs and fix unexpected problems before production commences. The cost-savings, in terms of time and money, can be significant.
TOOLING
In the production stage, our engineers tightly monitor the tool and pattern process to ensure the composite molds produced are of the highest quality, with impeccable dimensional accuracy

Project Management
Our project managers have proven skills across a range of high value and complex projects and work with customers worldwide to deliver on time and within budget. They analyse and track schedules, plan labour and material resources, administer costs, and provide complete visibility, informed advice and real time project updates at every stage. Many of our customers we have worked with over many years and on multiple projects. They continue to select mouldCAM as their Computer Aided Manufacturing partner because of our consistent track record for on time, on budget delivery.
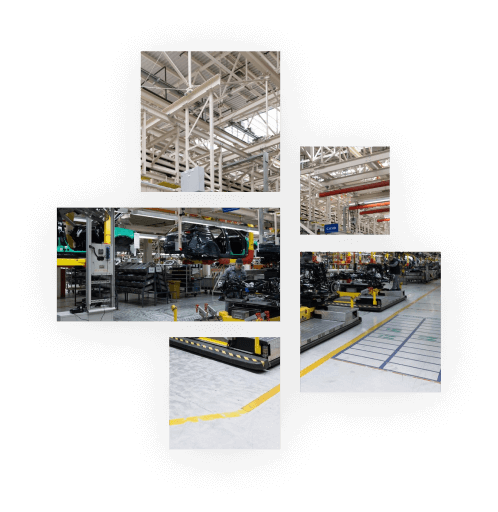
Manufacturing Facilities
FRP Technologies operates manufacturing and engineering facilities in the China and Sri Lanka with a combined production capacity of over 6,300 square meters/67,813 square feet.
- 2D & 3D profiling
- Free form and solid CAD modelling and drafting
- Reverse Engineering
- 5 axis CNC pattern machining
- GRP plugs, composite molds and composite tooling
- Closed molding RTM manufacturing
- Vacuum infusion
- Prototype development
- Parts production runs
- Prepreg manufacturing
- High temperature curing
- Assembly and fit out
- Spray painting and lacquering
- Custom packing, shipping
Our Certificates
ISO 9001:2015 Certified
At F R P Technologies (Pvt) Ltd, we are proud to be certified with the internationally recognized ISO 9001:2015 standard. This certification reflects our commitment to delivering high-quality products and maintaining a robust quality management system, ensuring customer satisfaction and continuous improvement across all our products.
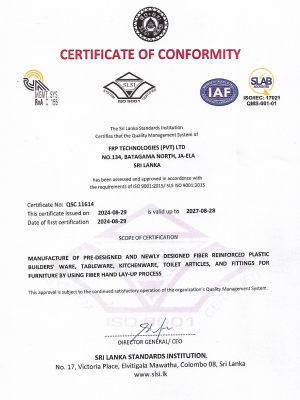
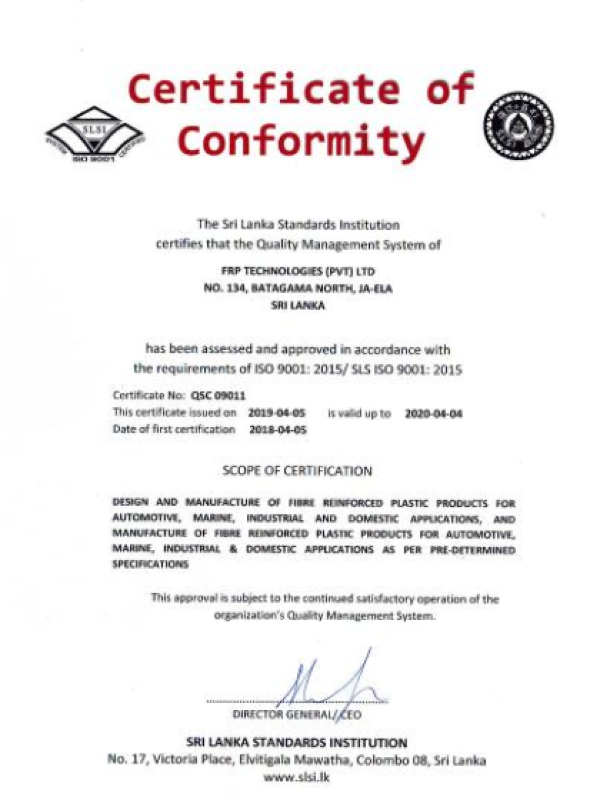




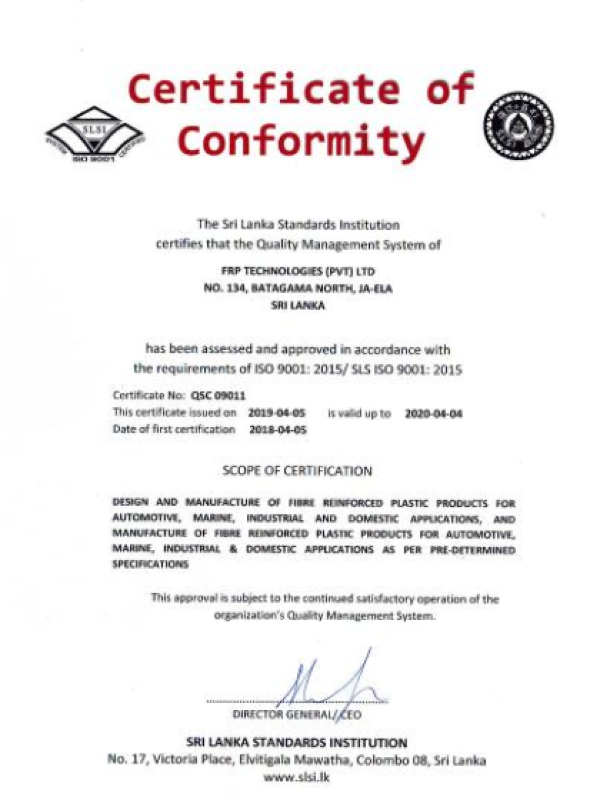
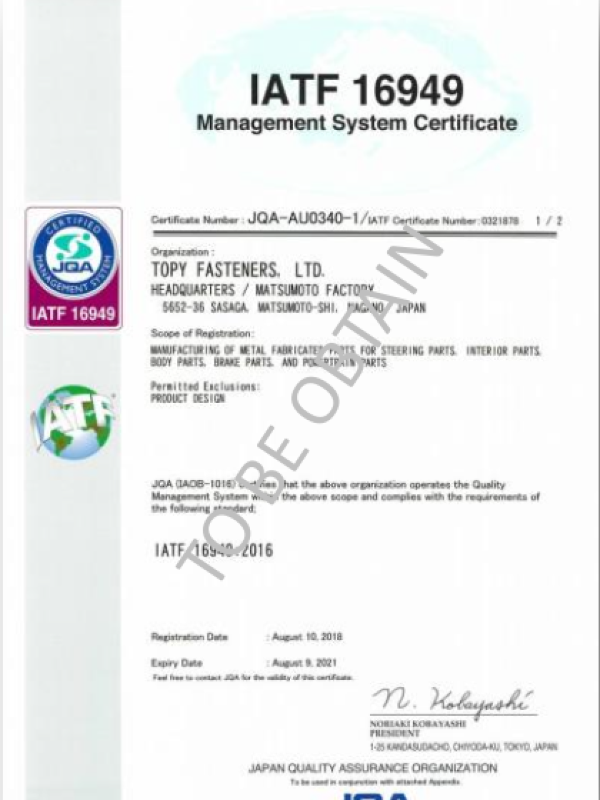
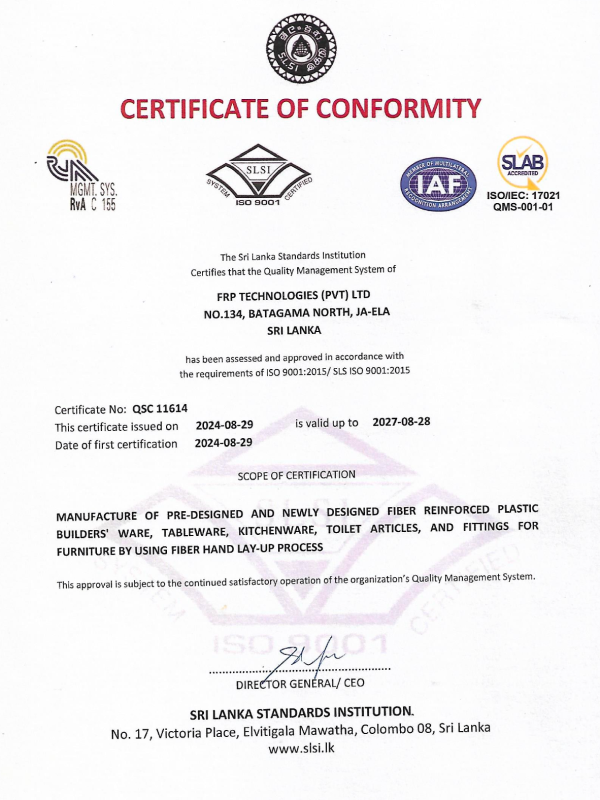
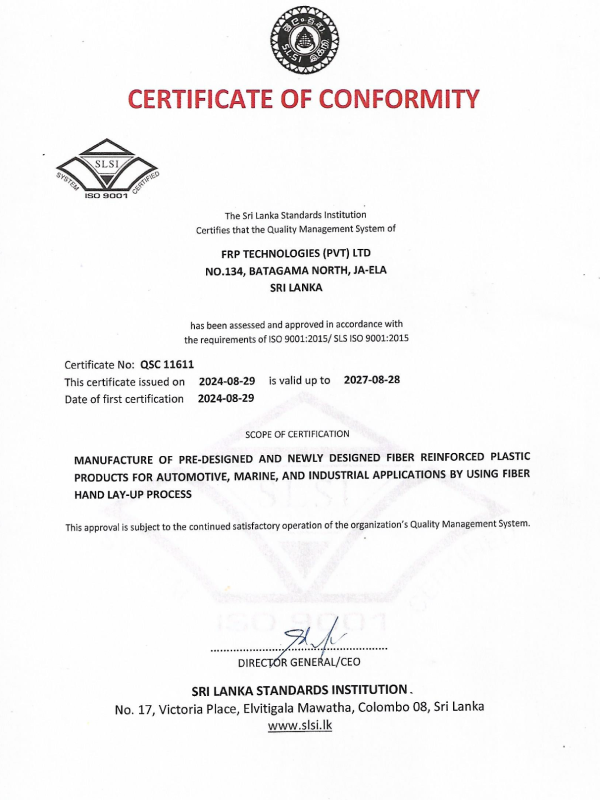
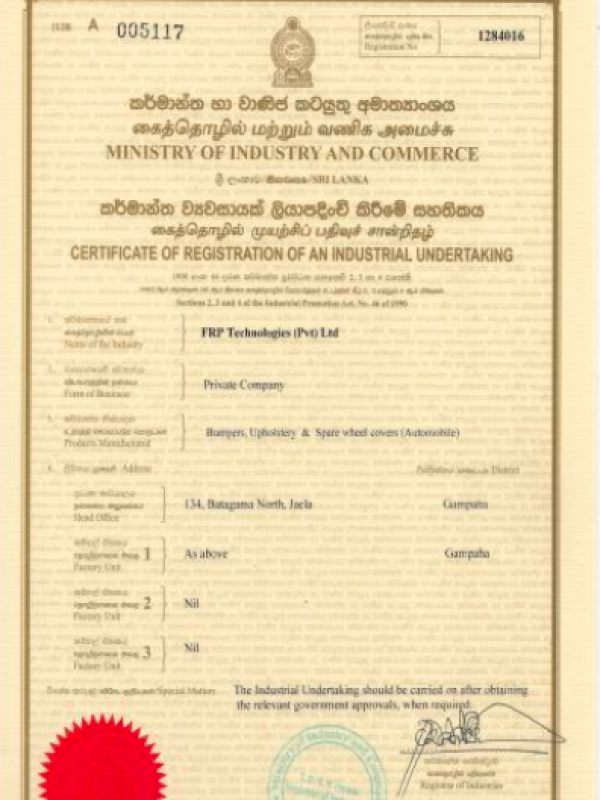
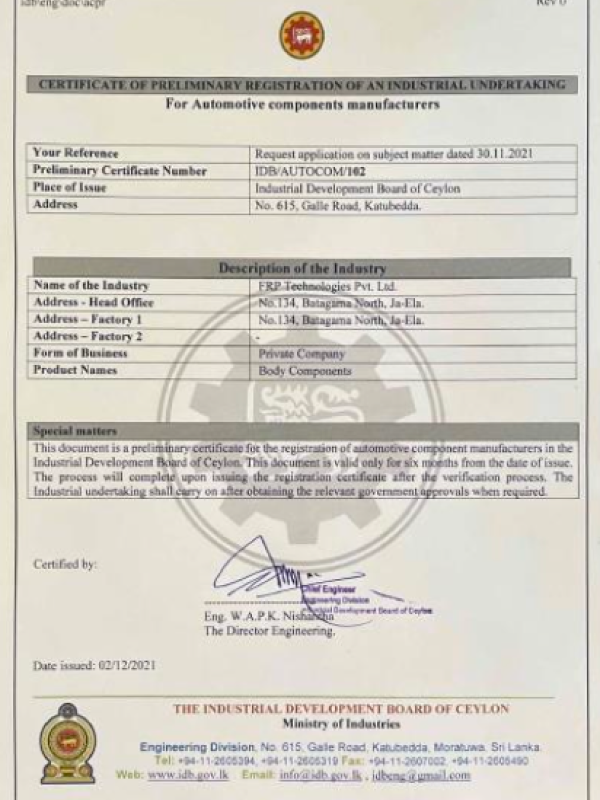
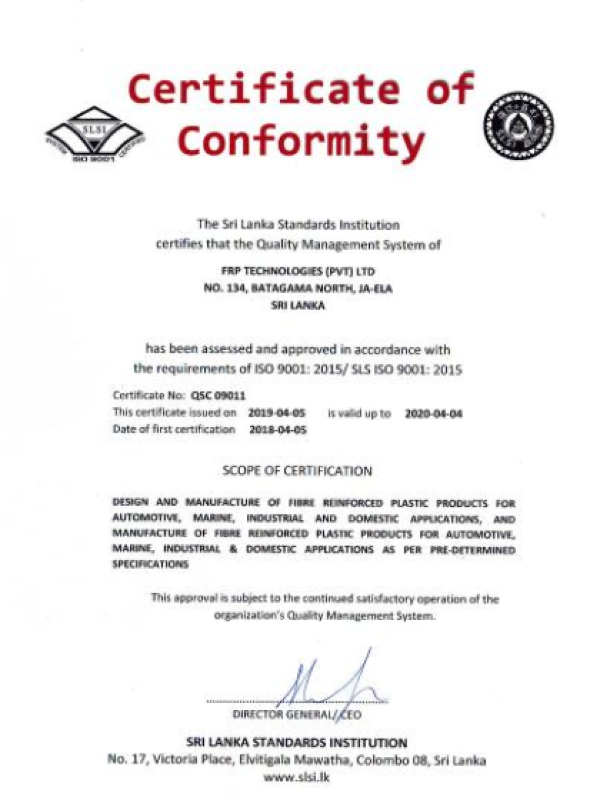
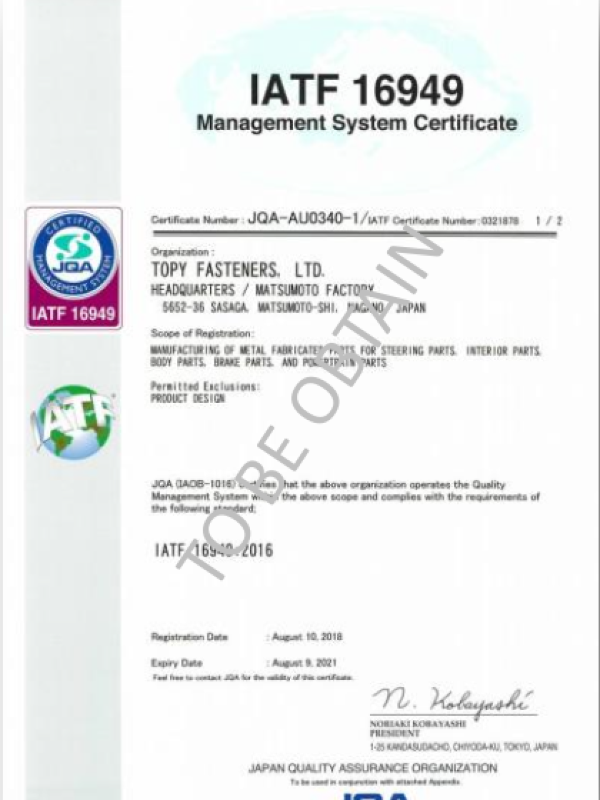
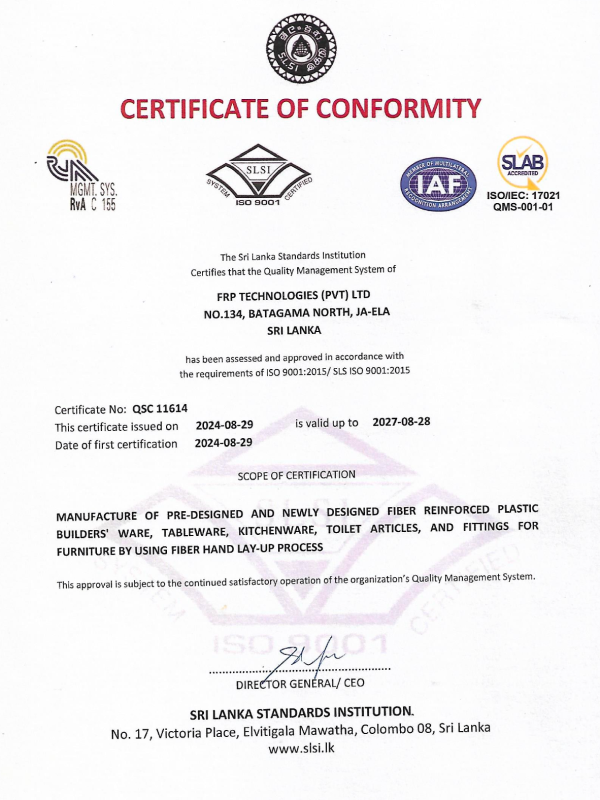
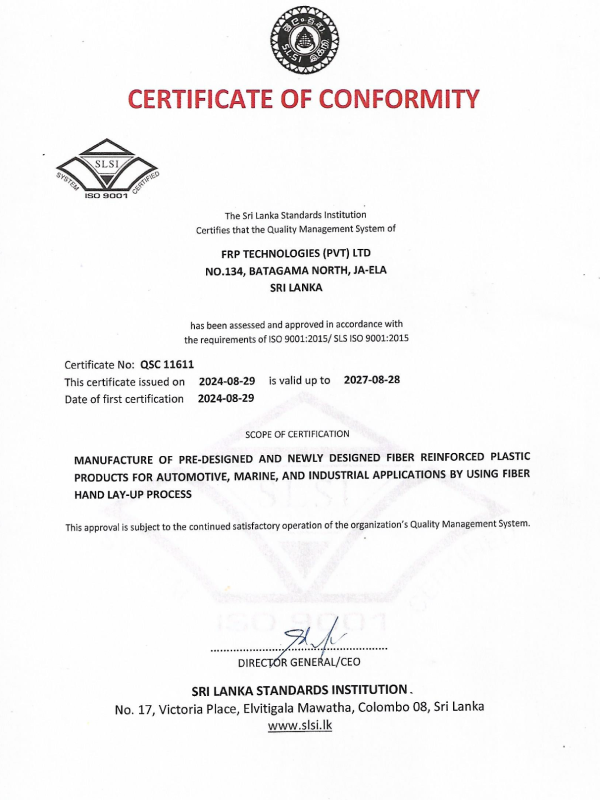
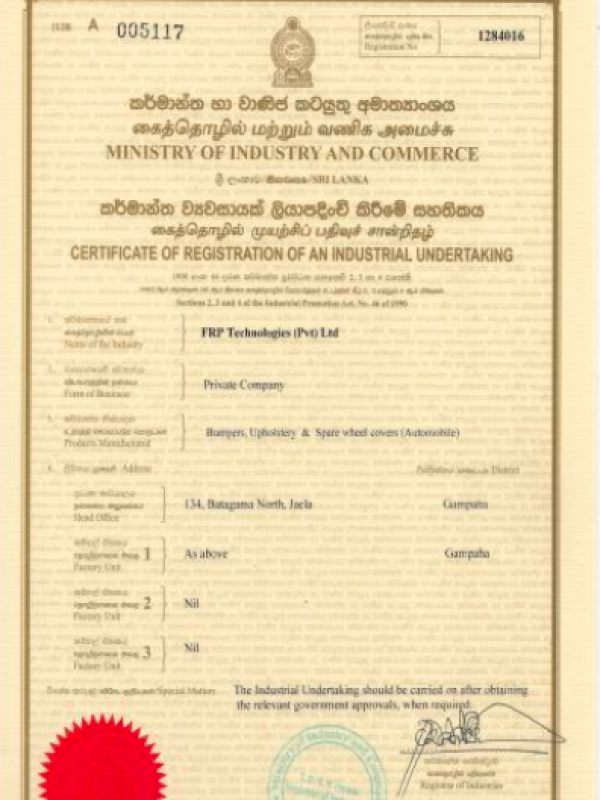
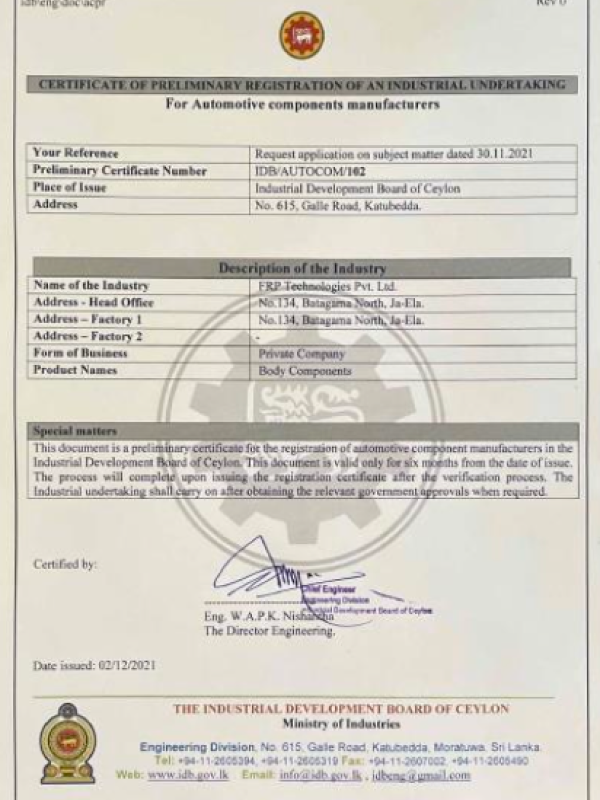